Massive Project. Strict Target Dates.
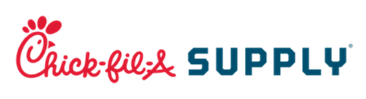

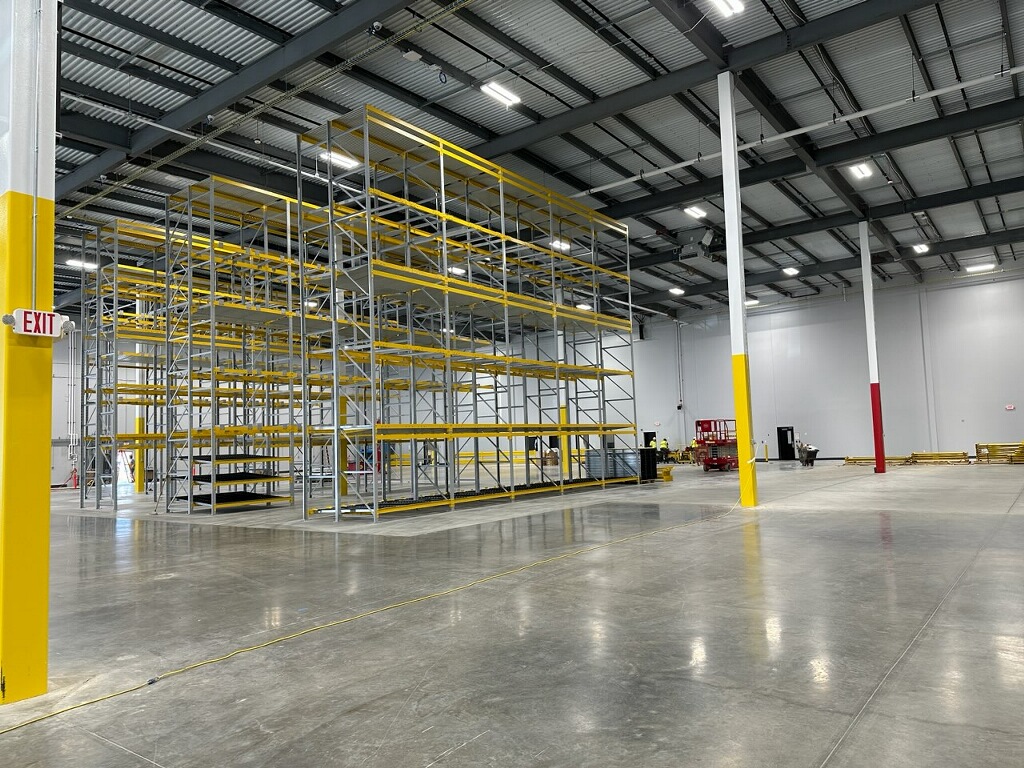
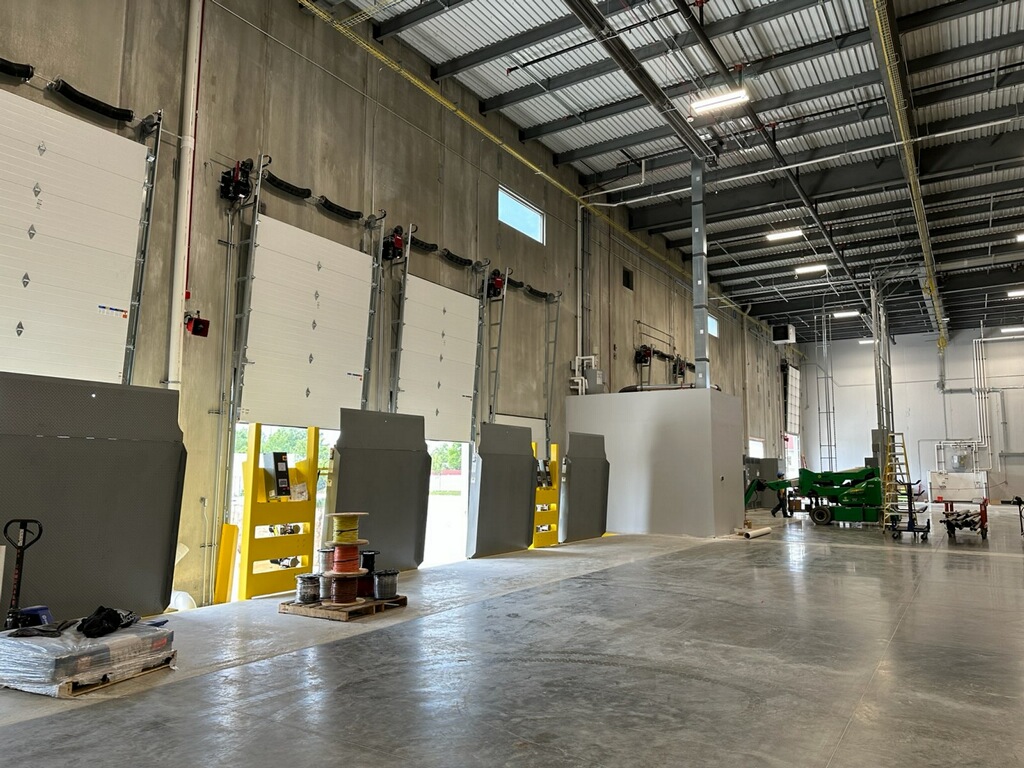
Harrington Electric Co. is thankful for its longtime member affiliation with Federated Electrical Contractors (FEC), an international network of leading electrical contractors.
FEC members were instrumental in initiating our relationship with Chick-fil-A and facilitating our involvement in this project.
Interesting Chick-fil-A Bites
- S. Truett Cathy founded Chick-fil-A in 1967, setting up his first restaurant in Atlanta.
- The “A” at the end of “Chick-fil-A” isn’t just a play on the word “fillet.” It means Grade A.
- There are only three states that don’t have a Chick-fil-A: Alaska, Hawaii and Vermont.
- Chick-fil-A is the largest purchaser of Sunkist lemons in the entire world. (They’re used to make its popular lemonade)
- The company is the largest buyer of peanut oil in the country.
- According to Chick-fil-A, waffle fries are its most popular menu item.
In an effort to keep up with its exploding growth, Chick-fil-A’s support arm, called Chick-fil-A Supply, has been rapidly expanding through the development and construction of massive distribution warehouses in a number of cities nationwide.
One of those locations is in Bedford Heights, Ohio, where the restaurant chain has leased a new, 150,000 square-foot spec shell structure and is completing a build-out of nearly 100,000 square feet of warehouse and office space.
When the facility is completed this month, Chick-fil-A Supply will be fully capable of ensuring that its 80-plus restaurants throughout the region will have the food, products and supplies needed to serve its customers on a daily basis.
Meeting the August, 2023 deadline (and a host of benchmarks leading up to the deadline) has been the primary objective for the Harrington Electric Co. team, which started working on the project in January, 2023. With a professional team of up to 27 electricians at times working seven days a week (or roughly 1,000 man-hours each week), Harrington completed numerous project components that were vital to ensure the facility’s scheduled opening.
According to Jerry Strand, Vice President of Electrical Construction for Harrington, the multi-faceted project involved a host of professional services that included the installation of:
- All electrical, distribution feeders and lighting throughout the 90,000+ square-foot warehouse (including freezers and coolers) and 10,000 square-foot office space;
- All security systems and card access systems in the building;
- The facility’s fire detection and alarm system;
- Gas monitoring systems;
- Electrical components required in the vehicle maintenance area;
- Controllers for 18 individual dock doors and levelers;
- A 2,500kw back-up generator, to be installed in later this fall.
Far from being routine installations, the project called for special equipment in some instances, such as the use of big lifts to access areas where ceilings heights exceeded 40-feet.
Supply chain challenges and very tight production schedules also had to be reckoned with. “There were many times when materials and supplies didn’t arrive on schedule, but that didn’t mean that the work stopped or the project goal posts moved,” said Strand. “Our team got really good at working around intermittent supply chain delays to meet the strict deadlines for this project and complete assigned tasks on schedule.”
With engineering details sometimes switching course during the project, it was necessary for the team to re-adapt and re-work on short notice, explained Strand. “In some instances, the project began when drawings were only 60% complete, and continued as required as designs were still in process in order to keep on schedule,” he said. “We had boots on the ground as designs were being finalized.”
Enhancing Facility Security
On the technology end, our illustrious Telecommunications and Voice-Data-Video team also contributed mightily to the project, providing security access control and CCTV camera systems throughout the facility.
The project has required installation of the latest security equipment, and cabling to the terminations at the rack and to a multitude of station ends.
This portion of the project will take an estimated six months to complete, according to Bob Laurenti, vice president of Harrington Electric’s Telecommunications division, and will add a high level of security in and around the building.
The end result of this massive project is an innovative, state-of-the-art distribution center that is fully equipped to respond to the daily needs of every Chick-fil-A restaurant in the state while keeping customers happy, and fulfilling the company’s mantra to “Eat Mor Chikin®.”